RTO waste gas incineration system
datetime:2019-12-20 Hits:1040 |
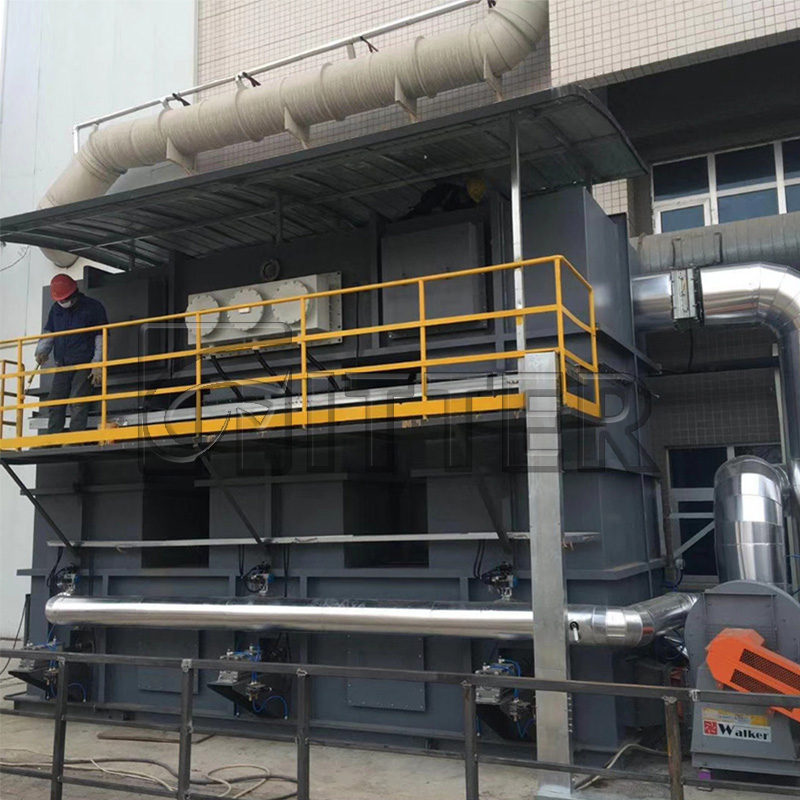
Regenerative thermal incinerator English name is "Regenerative Thermal Oxidizer", abbreviated as "RTO", RTO waste gas treatment product, is an energy-saving, high-efficiency, safety and environmental protection device for processing high concentration of volatile organic waste gas. The principle is that the exhaust gas is heated above 800 ° C, and the organic substances in the exhaust gas undergo an oxidation reaction at a high temperature, so that the hydrocarbons in the exhaust gas are oxidized to CO2 and H2O and directly discharged into the atmosphere. The incinerator is composed of three reinforced and insulated rooms. Part of the room is filled with high-temperature ceramic heat storage materials. The incinerator uses natural gas to maintain the set temperature of the combustion chamber in the furnace. The switching valve and duct passage located next to the RTO control the direction of exhaust gas in and out. The mode of this direction switching is completed by PLC control. This periodic switching control of PLC greatly improves the system heat recovery efficiency. Generally, the cycle time of a switching action is about 2 to 4 minutes. The exhaust gas enters the oxidation chamber through the heat recovery chamber. In this process, the high-temperature thermal storage ceramics will preheat the inlet exhaust gas and then introduce it into the catalytic furnace catalyst bed. When the exhaust gas passes through the thermal storage bed, the temperature rises sharply. After the oxidation reaction occurs in the oxidation chamber, high-temperature clean gas will pass through and heat the heat storage bed on the other side. In order to improve the heat recovery efficiency of the thermal storage bed, the system controls the operation of the double-cut damper by PLC to switch the flow direction of exhaust gas. This periodic switching makes the temperature more uniformly distributed throughout the oxidation furnace body. When the process air volume is at a sufficient concentration of volatile organic gas (3 ~ 4% minimum explosion limit, LEL), the thermal energy formed by the oxidation of organic substances will maintain the combustion process by itself, without the need for additional thermal energy.


RTO exhaust gas treatment equipment features: ●Can handle almost all exhaust gases containing organic compounds ● Can handle organic waste gas with large air volume and low concentration ●Great flexibility in handling organic waste gas flow (nominal flow 20% ~ 120%) ●Can adapt to changes and fluctuations in the composition and concentration of VOCs in organic waste gas ●Not sensitive to small amounts of dust and solid particles entrained in the exhaust gas ●Highest thermal efficiency among all thermal combustion purification methods (> 95%) ●Self-heating operation without the need to add auxiliary fuel under appropriate exhaust gas concentration conditions ●High purification efficiency (three rooms> 99%) ●Low maintenance workload and safe and reliable operation ●Organic deposits can be removed periodically and the heat storage body can be replaced ●Less pressure loss throughout the device ●Long device life
|
|
RTO waste gas incineration system |
datetime:2019-12-20 Hits:1040 |
Product description |
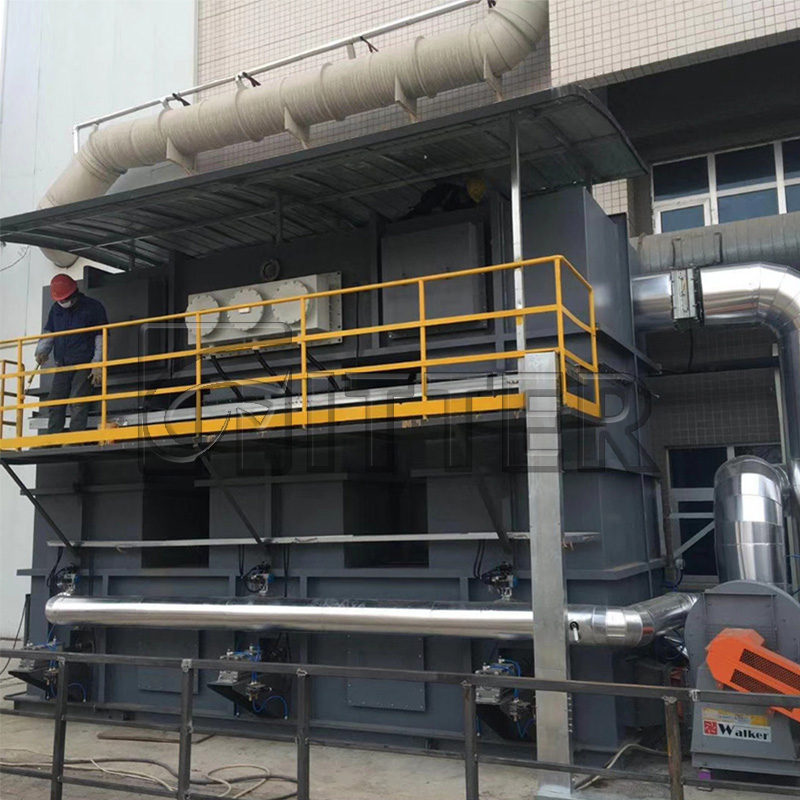
Regenerative thermal incinerator English name is "Regenerative Thermal Oxidizer", abbreviated as "RTO", RTO waste gas treatment product, is an energy-saving, high-efficiency, safety and environmental protection device for processing high concentration of volatile organic waste gas. The principle is that the exhaust gas is heated above 800 ° C, and the organic substances in the exhaust gas undergo an oxidation reaction at a high temperature, so that the hydrocarbons in the exhaust gas are oxidized to CO2 and H2O and directly discharged into the atmosphere. The incinerator is composed of three reinforced and insulated rooms. Part of the room is filled with high-temperature ceramic heat storage materials. The incinerator uses natural gas to maintain the set temperature of the combustion chamber in the furnace. The switching valve and duct passage located next to the RTO control the direction of exhaust gas in and out. The mode of this direction switching is completed by PLC control. This periodic switching control of PLC greatly improves the system heat recovery efficiency. Generally, the cycle time of a switching action is about 2 to 4 minutes. The exhaust gas enters the oxidation chamber through the heat recovery chamber. In this process, the high-temperature thermal storage ceramics will preheat the inlet exhaust gas and then introduce it into the catalytic furnace catalyst bed. When the exhaust gas passes through the thermal storage bed, the temperature rises sharply. After the oxidation reaction occurs in the oxidation chamber, high-temperature clean gas will pass through and heat the heat storage bed on the other side. In order to improve the heat recovery efficiency of the thermal storage bed, the system controls the operation of the double-cut damper by PLC to switch the flow direction of exhaust gas. This periodic switching makes the temperature more uniformly distributed throughout the oxidation furnace body. When the process air volume is at a sufficient concentration of volatile organic gas (3 ~ 4% minimum explosion limit, LEL), the thermal energy formed by the oxidation of organic substances will maintain the combustion process by itself, without the need for additional thermal energy.


RTO exhaust gas treatment equipment features: ●Can handle almost all exhaust gases containing organic compounds ● Can handle organic waste gas with large air volume and low concentration ●Great flexibility in handling organic waste gas flow (nominal flow 20% ~ 120%) ●Can adapt to changes and fluctuations in the composition and concentration of VOCs in organic waste gas ●Not sensitive to small amounts of dust and solid particles entrained in the exhaust gas ●Highest thermal efficiency among all thermal combustion purification methods (> 95%) ●Self-heating operation without the need to add auxiliary fuel under appropriate exhaust gas concentration conditions ●High purification efficiency (three rooms> 99%) ●Low maintenance workload and safe and reliable operation ●Organic deposits can be removed periodically and the heat storage body can be replaced ●Less pressure loss throughout the device ●Long device life
|
|
Prev:
RTO incineration system
|
Next:
RTO incineration system
|
Back>> |
|